The unsung heroes of metalworking, press brakes, bend and shape the skeletal structures of our modern world. Just as a painter relies on their brush, metalworkers depend on the press brake to transform flat sheets into forms of strength and utility.
What is a Press Brake?
A press brake is a formidable machine at the heart of metal fabrication. It’s a tool that applies significant force to metal, enabling precise bends. This apparatus has evolved significantly since its inception, growing from simple manual mechanisms to complex CNC machines.
Key Components of a Press Brake
Control System: The brain of the operation, orchestrating the machine’s movements.
Ram: The moving upper part that presses the metal down.
Die and Punch: Tools that work in tandem to shape the metal as the ram descends.
Backgauge: A positioning system ensuring metal sheets are aligned correctly for bending.
How Does a Press Brake Operate?
The dance of metal shaping begins with a meticulously orchestrated sequence of movements, each guided by the machine’s control system.
The Bending Process Explained
Metal is placed on the die, the punch is lowered by the ram, and precise pressure crafts the metal into the desired angle.
Why are Press Brakes Indispensable in Metal Fabrication?
In the symphony of metal fabrication, the press brake is the maestro, offering:
Precision: Hitting the mark within fractions of a millimeter.
Efficiency: Speedy production without sacrificing quality.
Versatility: Adaptable to various metals and shapes.
What Metals Can Be Shaped Using a Press Brake?
Aluminum: Lightweight yet sturdy, perfect for aerospace components.
Stainless Steel: Resistant to corrosion, ideal for medical devices.
What Are the Different Types of Press Brakes?
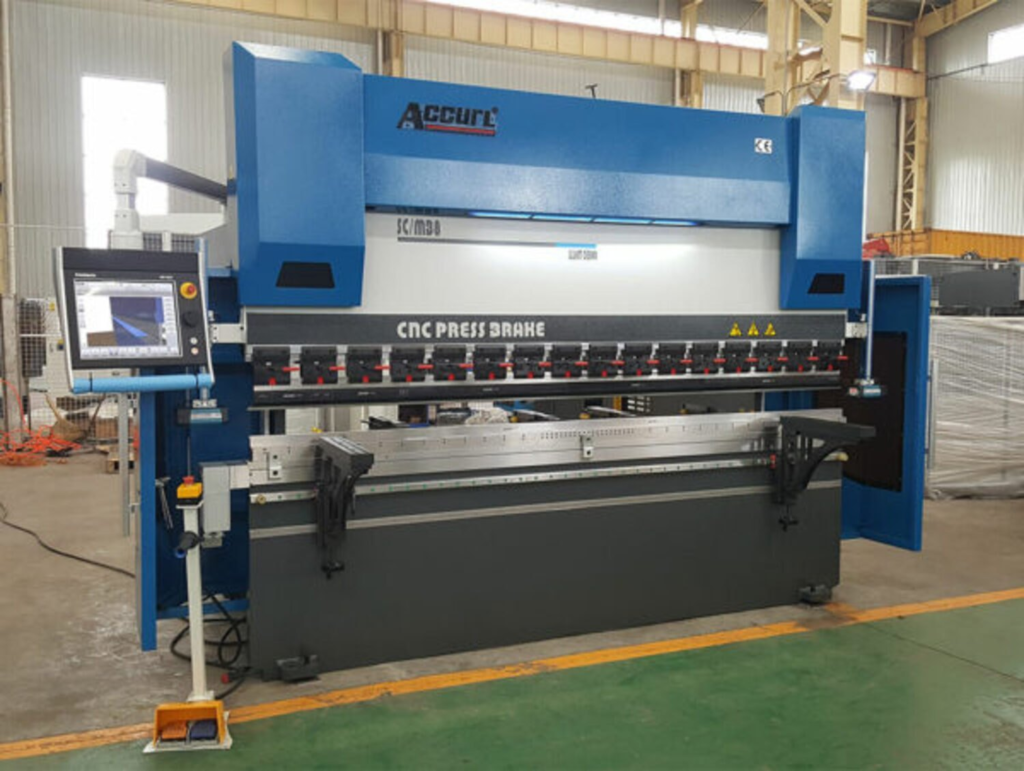
From the rugged hydraulic to the swift servo-electric, each type of press brake brings its own strengths to the table.
Hydraulic Press Brakes machines: The workhorses, known for power.
Mechanical Press Brakes: The classics, prized for simplicity.
Pneumatic Press Brakes: The agile ones, offer speed.
Servo-Electric Press Brakes: The modernists, synonymous with precision.
What Are the Capabilities of Press Brakes?
The capabilities of press brakes are as varied as the metals they mold, with bending lengths stretching up to meters and forces in the hundreds of tons.
What is the Maximum Thickness a Press Brake Can Handle?
Metrics reveal they can manipulate metals up to several inches or dozens of millimeters thick.
Press Brake Safety Protocols
Safety is paramount, and a set of protocols ensures the harmonious operation of man and machine.
How to Ensure Safety While Operating a Press Brake?
Strict adherence to safety gear and guidelines is the shield against the might of the press brake.
Press Brake Maintenance and Upkeep
The longevity of a press brake is secured through vigilant maintenance, from lubrication to alignment checks.
Troubleshooting Common Press Brake Issues
Common problems are often simple to fix with the right know-how, such as realigning a backgauge or recalibrating the control system.
Advanced Techniques in Press Brake Forming
Precision bending is an art, requiring a keen understanding of the machine’s capabilities and the metal’s properties.
How to Achieve Precision in Metal Bending with Press Brakes?
Advanced settings and the operator’s finesse merge to create bends that meet the strictest tolerances.
The Role of Press Brakes in Various Industries
Press brakes shape the bones of industries, from the sleek fuselage of aircraft to the robust beams in construction.
- Aerospace
- Automotive
- Construction
- Manufacturing
Innovations in Press Brake Technology
The future of press brakes is being forged with each technological leap, from enhanced controls to automated systems.
What Are the Latest Trends in Press Brake Technology?
The horizon of metalworking is expanding with the integration of IoT and the advent of more energy-efficient systems.
Choosing the Right Press Brake for Your Metalworking Needs
Selecting a press brake is a strategic decision, balancing capabilities with the specific demands of projects.
Comparison of Top Press Brake Manufacturers
Key players in the industry offer a range of solutions, from Amada’s precision to Trumpf’s innovation.
Alternatives to Press Brakes in Metal Shaping
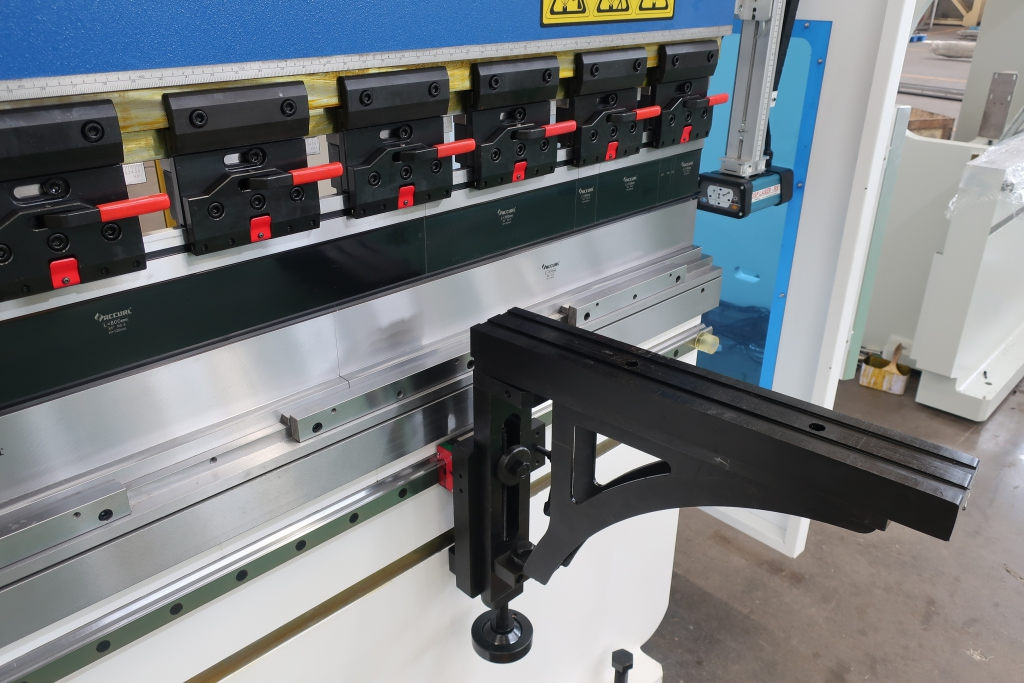
While press brakes reign supreme, other methods like laser cutting and 3D printing offer complementary possibilities.
Conclusion
Press brakes remain the cornerstone of metalworking, continuously evolving to meet the challenges of tomorrow’s designs.
Blog Received On Mail