The world of plastic manufacturing is changing fast. New technologies are popping up all the time, promising to make things better, cheaper, and more eco-friendly. However, for many manufacturers, keeping up with these changes can feel overwhelming. This article will break down some of the most important new technologies in plastic manufacturing and offer practical advice on how to adapt to them.
3D Printing
Let’s start with 3D printing, also known as additive manufacturing. This technology has been around for a while, but it’s getting better and more useful for plastic manufacturing all the time.
3D printing works by building up layers of plastic to create objects. It’s great for making complex shapes that would be hard to make with traditional methods. It’s also perfect for creating prototypes quickly or making small batches of custom items.
To adapt to 3D Printing, consider these steps:
- Invest in a 3D printer that fits your needs. There are many different types, from small desktop models to large industrial machines.
- Train your staff to use 3D printing software and equipment. This might involve sending them to workshops or bringing in experts to teach them.
- Look at your product designs. Are there ways you could improve them using 3D Printing? Maybe you could make them lighter, stronger, or more complex.
- Start small. Try using 3D Printing for prototypes or small production runs before you commit to larger projects.
By embracing this technology, you can open up new possibilities for product design and customization.
Advanced Injection Molding
The plastic injection molding machine has been around for a long time, but it’s still evolving. New advances are making it faster, more precise, and more energy-efficient.
- Some of the new technologies in injection molding include:
- All-electric machines that are more energy efficient than hydraulic ones
- Micro-molding for making tiny parts
- Gas-assisted molding for making hollow parts
- Multi-material molding for making complex products in one step
To take advantage of these new technologies:
- Assess your current injection molding equipment. How old is it? How efficient? This will help you decide if it’s time to upgrade.
- Look at your products. Could they be improved with newer injection molding techniques?
- If you decide to invest in new equipment, make sure your staff gets thorough training on how to use it.
- Consider the energy efficiency of new machines. They might cost more upfront but could save you money on energy bills in the long run.
Upgrading your injection molding capabilities can help you produce higher-quality products faster and at a lower cost.
Bioplastics
Next up are bioplastics. These are plastics made from plants or other renewable sources instead of oil. They’re becoming more popular as people look for ways to reduce their environmental impact.
Bioplastics can be used to make many of the same products as traditional plastics. Some are biodegradable, which means they break down naturally over time. Others are just as durable as regular plastics but made from renewable sources.
To start using bioplastics in your manufacturing:
- Research different types of bioplastics to find ones that suit your products.
- Test these materials to make sure they meet your quality standards.
- You might need to adjust your manufacturing equipment to work with bioplastics. Plan for this and budget accordingly.
- Consider the whole life cycle of your products. If you’re using biodegradable bioplastics, think about how customers will dispose of them.
- Use your switch to bioplastics as a marketing opportunity. Many customers like eco-friendly products.
As consumer demand for eco-friendly products grows, adopting bioplastics could give your business a competitive edge.
Chemical Recycling
Chemical recycling is a new way to deal with plastic waste. Instead of just melting and reshaping plastics, it breaks them down into their basic chemical building blocks. These can then be used to make new plastics or other products.
This technology could help solve the problem of plastic waste by making it easier to recycle more types of plastic. It could also provide manufacturers with a new source of raw materials.
To get involved with chemical recycling:
- Look for chemical recycling facilities in your area. You might be able to partner with them to recycle your waste or source recycled materials.
- If there aren’t any nearby, consider investing in your own chemical recycling equipment. This could be a big investment, but it might pay off in the long run.
- Start thinking about how you could use chemically recycled materials in your products. You might need to adjust your manufacturing processes.
- Educate your customers about chemical recycling. If they understand the benefits, they might be more willing to buy products made from recycled materials.
By getting involved early, you can position your company as a leader in sustainable manufacturing practices.
Smart Manufacturing
Smart manufacturing, sometimes called Industry 4.0, is all about using technology to make factories smarter and more efficient. This can involve things like sensors that monitor your equipment, artificial intelligence that predicts when maintenance is needed, or data analytics that help you optimize your production.
Adapting to smart manufacturing can be a big change, but it can also bring big benefits. Here’s how to get started:
- Start by identifying areas where you could benefit from more data. Maybe you want to track energy use, monitor product quality, or optimize your supply chain.
- Invest in sensors and data collection systems. These will be the foundation of your smart manufacturing setup.
- Look into software that can help you analyze and use your data. There are many options out there, from simple dashboard tools to complex AI systems.
- Train your staff to use these new tools. They’ll need to understand not just how to operate them but how to use the insights they provide.
- Be prepared to make changes based on what your data tells you. The real value of smart manufacturing comes from using your new insights to improve your processes.
The initial investment may be significant, but the long-term benefits in terms of productivity and competitiveness can be substantial.
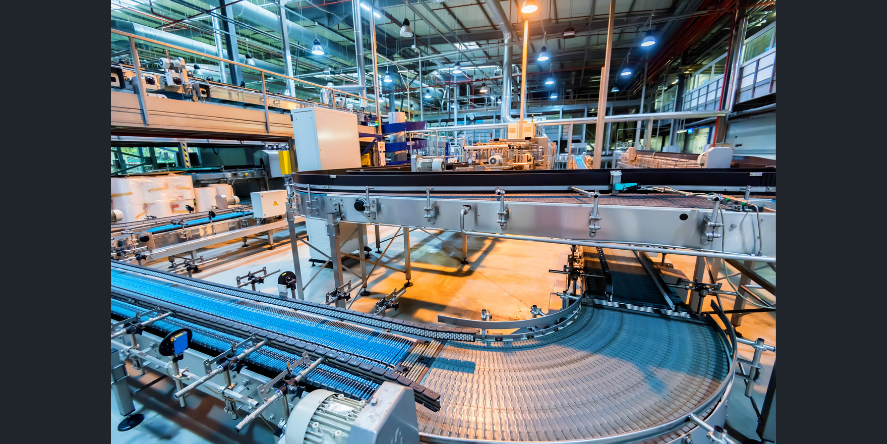
Nanotechnology
Nanotechnology involves working with materials at an incredibly small scale – we’re talking about particles that are billionths of a meter in size. In plastic manufacturing, nanoparticles can be added to plastics to give them new properties. For example, they might make the plastic stronger, more heat-resistant, or able to conduct electricity.
To start using nanotechnology in your manufacturing:
- Research how nanoparticles could improve your products. There are many different types of nanoparticles, each with different effects.
- Be aware of safety concerns. Because nanoparticles are so small, there are some worries about their potential health effects. Make sure you understand and follow all safety guidelines.
- You might need specialized equipment to work with nanoparticles. Plan for this investment.
- Consider partnering with a research institution or nanotechnology company. They can help you develop new materials and processes.
While it requires careful research and investment, the potential for innovation makes it a technology worth exploring.
Bringing It All Together
Adapting to new technologies in plastic manufacturing isn’t easy. It takes time, money, and effort. But it’s also necessary if you want to stay competitive and meet growing demands for efficiency and sustainability.
Here are some final tips for successfully adapting to new technologies:
- Stay Informed: Read industry publications, attend trade shows, and network with other manufacturers to keep up with the latest trends.
- Start Small: You don’t have to overhaul your entire operation overnight. Try piloting new technologies in one area of your business first.
- Involve Your Staff: They’ll be the ones working with these new technologies day-to-day. Get their input and make sure they’re on board with changes.
- Be Patient: Implementing new technologies takes time. Don’t expect instant results.
- Keep an Open Mind: The plastic manufacturing industry is always changing. What seems cutting-edge today might be standard practice tomorrow.
Adapting to new technologies in plastic manufacturing is crucial for staying competitive in a rapidly evolving industry.
Final Thoughts
By embracing new technologies and being willing to adapt, you can ensure that your plastic manufacturing business remains competitive and sustainable for years to come. The future of plastic manufacturing is exciting, and with the right approach, you can be a part of shaping it.
Blog received on email