SSAB starts a partnership in fossil-free steel applications with Oshkosh Corporation, one of the leading innovators of mission-critical vehicles and essential equipment, including heavy duty truck bodies, fire apparatus, access equipment and other specialty trucks.
Oshkosh Corporation will initially use the fossil-free steel for material with the aim to prototype advanced, environmentally sustainable refuse collection vehicles, and plans future research and development initiatives across multiple commercial vehicle product lines.
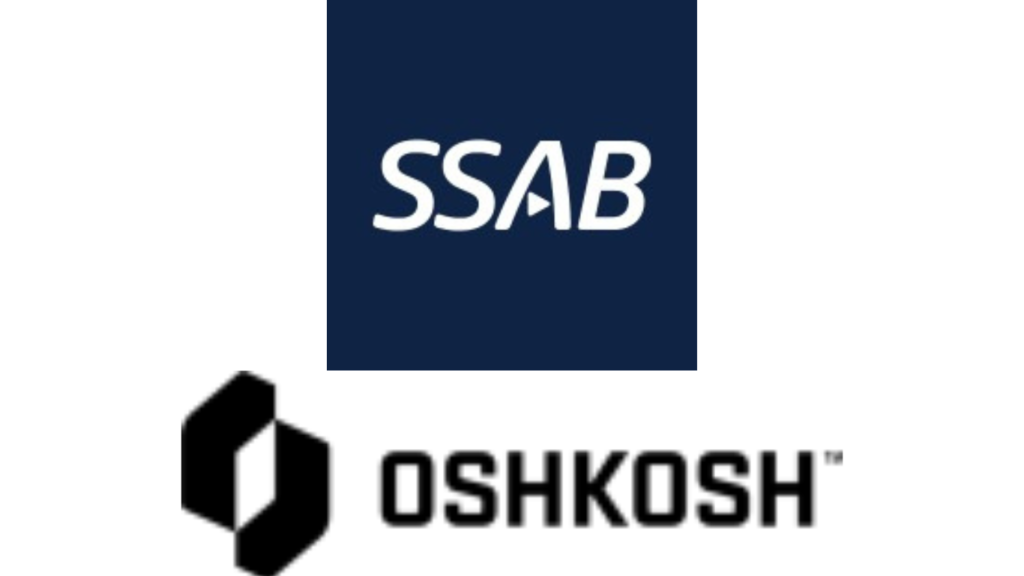
“We are very happy to welcome Oshkosh Corporation into our partner group to be the first in the United States to prototype fossil-free steel in commercial and industrial vehicles,” says Martin Lindqvist, President and CEO at SSAB. “Demand for fossil-free steel continues to increase globally. This step confirms our commitments to mitigate global climate change, and collaboration with forward-thinking organizations around the world for industry-leading change is how it will happen.”
“Creating a more sustainable future is central to our strategic vision,” says Brad Nelson, President of McNeilus Truck and Manufacturing and Senior Vice President of Oshkosh Corporation. “As a leader and innovator in the industries we serve, Oshkosh Corporation is proud to partner with SSAB on this global initiative as a next step in delivering high-performance, more sustainable products to our McNeilus Truck and Manufacturing customers.”
SSAB aims to deliver fossil-free steel to the market in commercial scale during 2026, and delivered the first steel made of hydrogen-reduced iron in 2021. SSAB works with iron ore producer LKAB and energy company Vattenfall in Sweden as part of the HYBRIT initiative to develop a value chain for fossil-free iron- and steel production, replacing coking coal traditionally needed for iron ore-based steelmaking, with fossil-free electricity and hydrogen. This process virtually eliminates carbon dioxide-emissions in steel production.
Oshkosh Corporation’s sustainability efforts include working to reduce the “use-phase” emissions of its products through higher fuel efficiency, alternative fuel and electrification. All product lines offer or are in the process of developing alternative powertrains, including fully electric, hybrid and compressed natural gas solutions that significantly reduce the carbon footprint. Moving the reductions from production and operations to the supply chain sourcing of carbon-free materials is a natural step to meeting 2030 goals.
